What is a Distributor Cap?
A distributor cap is a removable component that is used in spark ignition systems to cover both the distributor and the rotor. In addition to covering these components, and protecting them from contamination, distributor caps are also responsible for helping to distribute electrical current from an ignition coil to a set of spark plugs. Since distributor caps are wear items, they have to be replaced periodically as they wear out.
Contents
Components of a Distributor Cap
Although distributor cap designs can vary from one application to another, they all share a few basic components:
- a main housing (typically plastic)
- at least one contact/lead per cylinder
- a main contact point (to connect the rotor and coil)
The main body of a distributor cap is typically made from molded plastic that has a number of metal components built into it. A typical cap has one metal contact and post per cylinder and one central contact and post for the coil. The central contact is typically a spring-loaded carbon brush that mates with a central contact point on the rotor, which allows it to remain electrically connected while the rotor is spinning. The other contacts are spaced evenly around the perimeter of the cap, which allows the rotor to touch them as it spins.
Rather than having a central contact and post for the coil, some caps have two internal contacts. This is due to the fact that some vehicles have ignition coils that are located inside or on top of the distributor. Instead of using an external post and a coil wire, these coils are connected to a rotor by an internal connection inside the cap.
Other caps have slight variations in design due to the way that the engines of some vehicles are set up. Although most engines that use distributors are designed to only fire each spark plug on the combustion stroke of its corresponding cylinder, some engines use a waste spark ignition system. These ignition systems always fire two plugs at once: one on its combustion stroke and the other on its exhaust stroke. In order to account for this, distributor caps in waste spark ignition systems have half as many internal contacts as there are cylinders in the engine, and each contact is tied into two posts.
Another variation is found in vehicles that have two spark plugs per cylinder. Distributor caps in these ignition systems have one internal contact per cylinder, but each one connects to two posts. These posts are then connected to two spark plugs per cylinder via spark plug wires.
How does a Distributor Cap Work?
In order for an internal combustion engine to run properly, the spark plugs have to be activated in the correct firing order. This can be accomplished in a variety of different ways, but conventional mechanical and electronic ignition systems do it with a distributor, distributor cap, and a rotor. The distributor is the component that is actually responsible for correctly distributing spark, but it can’t do its job without the distributor and the rotor.
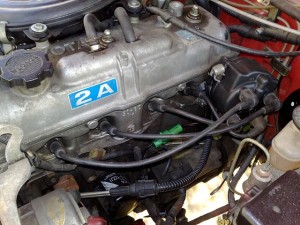
A distributor cap provides the electrical connection between the coil (located inside the distributor in this Toyota) and the spark plugs.
In conventional mechanical and electronic ignition systems, a distributor provides both a stationary base for a distributor cap and a source of rotational movement for a rotor. When a distributor cap is installed, it has to be lined up correctly on the distributor. This is typically accomplished via some type of keyway or other eccentric base design, as a properly oriented distributor cap is essential for the correct operation of an internal combustion engine.
If a distributor cap is properly installed, and the plug wires are attached to the proper spark plugs and distributor cap posts, then the plugs will be activated in the correct order and at the proper time. This is possible due to the fact that the rotor turns inside the distributor cap in time with the camshaft, which allows it to bridge one external post at a time with the central contact. When that happens, a circuit is completed between the coil and a spark plug, and the spark plug can ignite the air/fuel mixture in its cylinder.
Distributor Cap Failure
The two main factors that can lead to distributor cap failure are contamination and simple wear. If any contaminants are able to get inside the cap, they may interfere with its ability to distribute the high voltage pulses that it distributes to the spark plugs. This is especially true if water gets inside a cap, since water can cause the pulses to short directly to ground. Some distributor caps have o-ring seals or gaskets to prevent water and other contaminants from getting inside, but that isn’t always the case. If water or other contaminants do get inside a cap, the distributor and cap can be cleaned, blown out, or (in some cases) a water displacement spray can be used.
In most cases, distributor cap failure is due to the component simply wearing out. These components are wear items, which means that they are expected to wear out after a certain amount of time or usage. Caps typically fail due to worn contacts or buildup on the contacts, but it’s also possible for a cap to develop one or more carbon tracks that allow electrical current to short out to ground.
In any case, a distributor cap failure is typically rectified by simply replacing the component. While it is sometimes possible to get some more use out of a cap (and a rotor) by cleaning the contacts, an engine will typically run better (and more efficiently) with new components. Since the cap has to be removed to access the rotor, and these components tend to wear at roughly the same rate, it’s typically a good idea to replace them at the same time. The same is true of the points and condensor in mechanical spark ignition systems, and all of these components are often replaced together as preventative maintenance instead of waiting for one or more of them to fail.